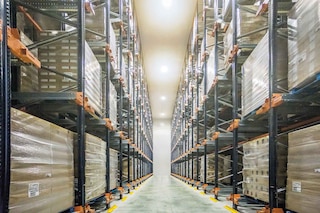
Minimum stock levels: definition and strategies
The classification of inventory into different types of stock helps a company monitor and streamline its operating stock levels for its supply chain. As orders are shipped, the products stored decrease in quantity. Taking into account these fluctuations, two key concepts emerge:
- Maximum stock level: determined by the warehouse’s storage capacity and the purchasing or procurement policy.
- Minimum operating stock level: indicates the point of inventory consumption at which goods need to be replenished, just before the safety stock is used.
The rule for minimum/maximum stock levels is one of the most deeply ingrained stock control methods in business. In our article, we’ll analyse its scope and limitations, showing you how to optimise minimum stock levels in your installation.
What is the minimum stock level? The minimum/maximum stock level rule
With the rule for minimum/maximum stock levels, a replenishment point is set and, as the SKUs are used up, they are reordered to complete the inventory.
Visually, therefore, they take the form of a sawtooth graph, with peaks representing the purchase of inventory and valleys showing the dispatch of these goods from the warehouse.
It’s a simple method to implement, and it can be automated with almost any ERP or WMS. In this way, when a SKU reaches the minimum stock level, the system issues a notification or automatic replenishment order, relieving managers from carrying out this task.
While there are various methods for setting minimum stock levels, in a nutshell, the main variables involved in calculating this parameter are:
- Demand forecasting: how many units of that particular SKU are consumed in a given period of time?
- Supplier lead time: how long does it take to process the order and for the goods to arrive at the warehouse?
- Order cost (and size) and supplier standards in this regard.
Graphic representation of stock levels
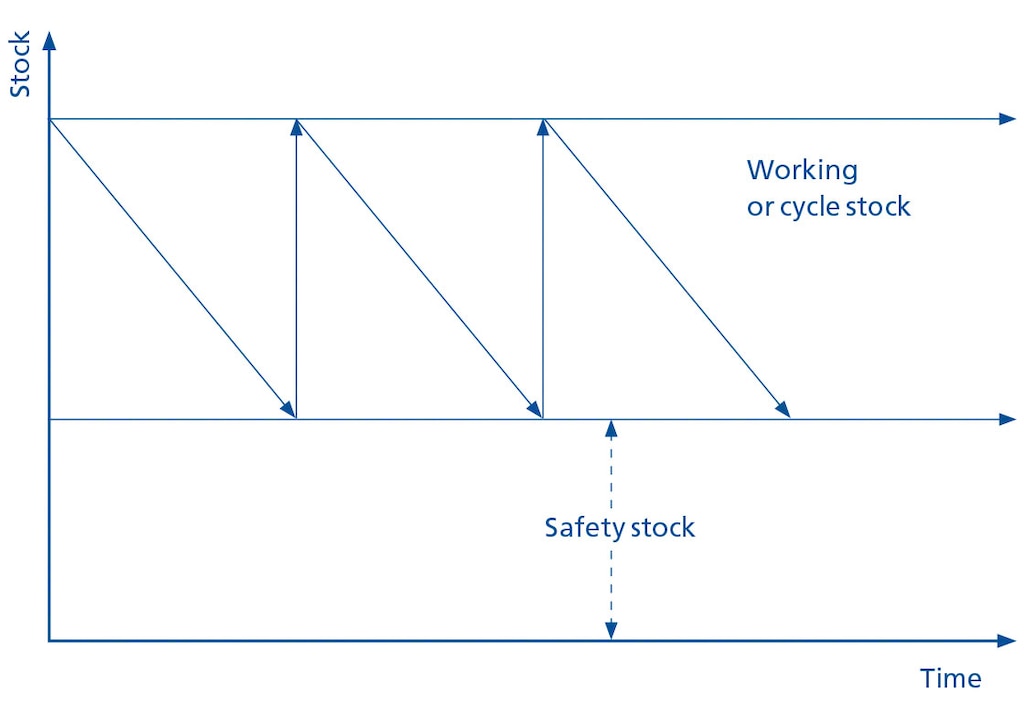
What are the limitations of the minimum/maximum stock level rule?
The rule for minimum/maximum stock levels is simple and easy to implement, which is why it’s applied by so many companies. Nevertheless, there are constraints on this guide that should be mentioned:
- It’s based on analysing each SKU individually, without taking into account overall inventory or supplier status. For example, there might be a supplier whose order policy requires the company to reach a particular spending level; however, this amount can be divided among all the products in the supplier’s catalog. With a minimum/maximum stock level approach, the order would be issued when the requisite cost was reached with a single SKU and not with a set of them, which could be more economically beneficial.
- It doesn’t always take into consideration product trends. Each SKU has a life cycle with various stages impact that demand: introduction, growth, maturity and decline. Unless the minimum/maximum stock level rule is under continuous manual review (which would mean missing out on the advantages of automation in this process), constant replenishment could lead to the accumulation of costly overstock.
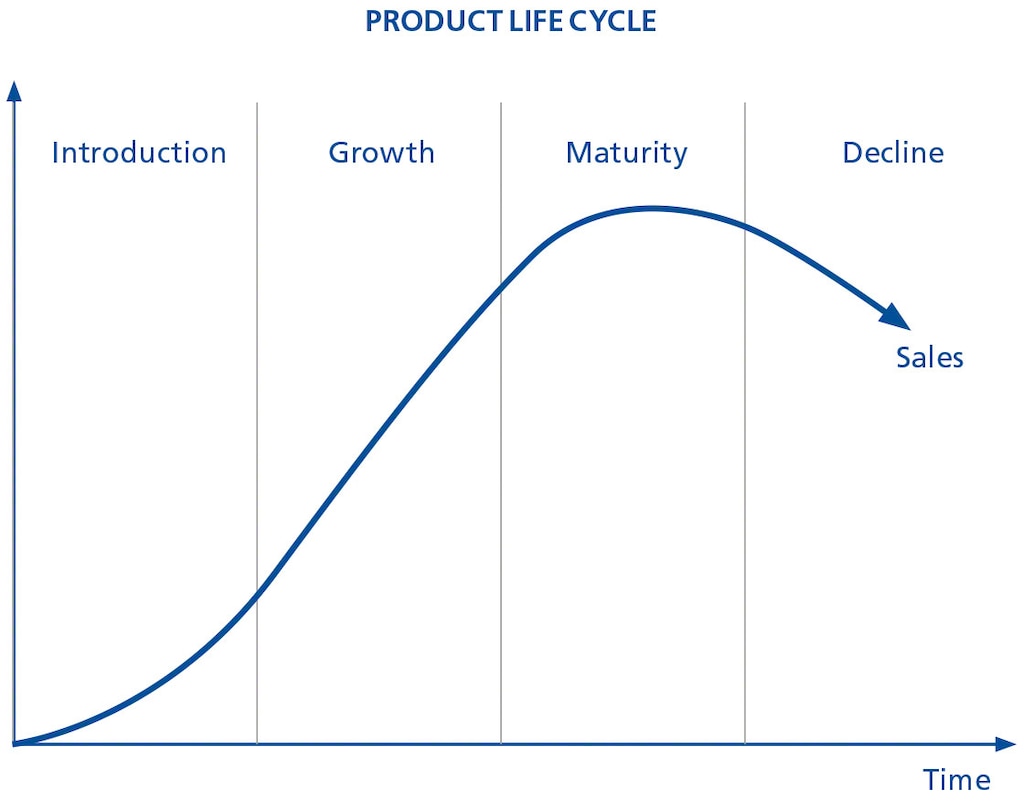
Advantages of improving minimum stock level management
One consequence of implementing a rigid minimum/maximum stock level policy is that you end up accumulating more inventory than necessary. In fact, optimisation of stored stock is one of the cornerstones of the Lean logistics methodology and its advantages are noteworthy:
- It reduces capital tied up in the holding of inventory, an investment that can be allocated to other items, thereby increasing the company’s liquidity.
- It cuts costs linked to maintaining that stock, which represent a significant sum within logistics storage costs. Optimisation also minimises the risk of storing low-turnover inventory that could suddenly become obsolete and lead to losses for the business.
- It frees up warehouse space so that it can be repurposed to expand the catalog, boost the capacity of the picking area, or hold the stock that’s really meant to be stored there.
So, how do you optimise your inventory to maintain minimum stock levels?
Well, here are some tips:
Classify and prioritise your inventory in the warehouse
Reviewing and categorising stored inventory according to stock turnover will bring to light products that haven’t sold well and are hindering overall stock management.
In this vein, warehouse management software enables you not only to implement cycle counts that check the accuracy of inventory data, but also to have a valuable historical record that will make the stock optimisation task much easier.
In addition, managing this information will be extremely helpful for prioritising minimum stock levels for your most important SKUs according to various logistics parameters: turnover, profit margins and procurement cost, among others. Thus, the minimum stock levels for each SKU should be set from a comprehensive perspective as opposed to an individual one: they all compete together for the same inventory procurement investment.
Plan beyond the minimum stock figures
On occasion, the minimum/maximum stock level rule works in a vacuum, especially if it’s been automated in such a way that it’s applied strictly when stocks hit their minimum level. Be that as it may, it’s advisable to plan replenishment orders bearing in mind factors that affect logistics operations, not only stock level figures.
If not, goods receipts in the installation might become overloaded. Additionally, if a purchase order placed with a supplier is set up for automatic dispatch, the company loses out on the advantages of goods consolidation and groupage.
In any case, the warehouse should be prepared to deal with such predicaments. Having a WMS makes it possible for the installation to process unplanned receipts and organise the subsequent location management of these goods.
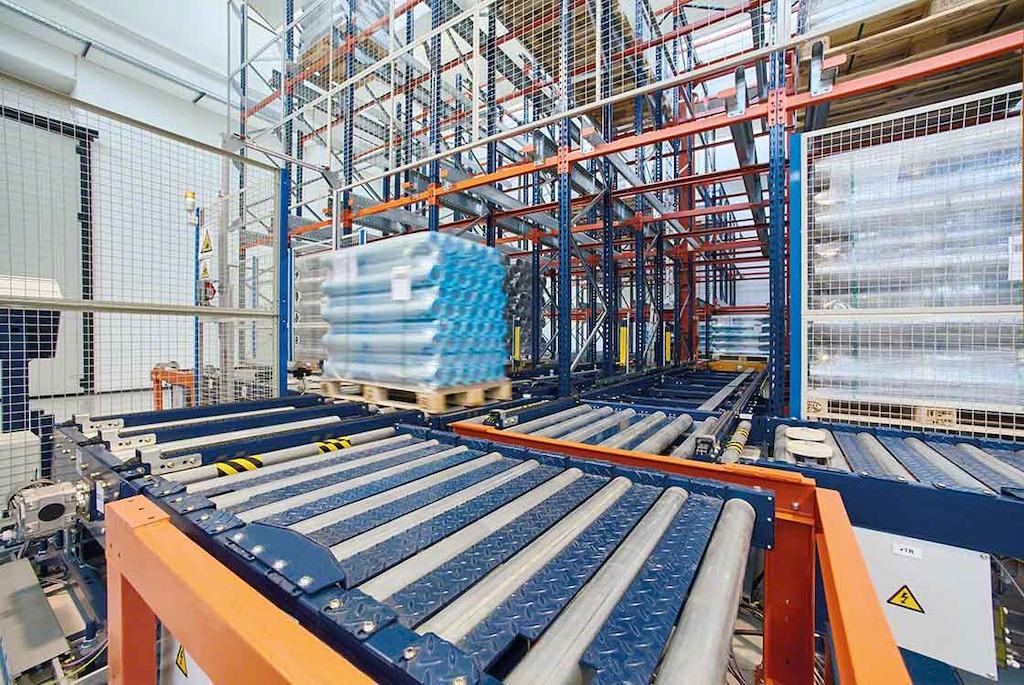
Streamline your warehouse by bringing down operating costs
The main function of inventory is to enable the company to respond to demand at the right time and in the right way. Despite strategies such as the just-in-time system, which aims to approach the zero-stock paradigm, storing goods is and will always be necessary for the proper functioning of the supply chain.
On the basis that there needs to be a minimum stock level, operating costs should be kept to a minimum: thus, you slash the time that the inventory needs to be stored. One practical way to do this is to work on warehouse efficiency, improving lead times. These can be divided into two types:
- Physical lead times: these refer to the time it actually takes to transport the goods from one place to another. Undoubtedly, automating processes such as goods movements in the installation frees up the operators to carry out more value-adding tasks.
- Information lead times: these relate to time spent on processing orders and picking lists and on organising each task in the correct order of priority. WMSs have been developed as powerful tools capable not only of lowering cycle times, but also of perfecting the execution of operations until they’re practically error-free.
In addition, monitoring the dynamic between the various stock levels in the warehouse is essential for, on the one hand, preventing those dreaded stockouts and, on the other, keeping safety stock levels under control.
WMSs also play a crucial role in this area, as they bring together all the major KPIs to make sound decisions. In this sense, Easy WMS’s Supply Chain Analytics Software module stands out.
The challenge of setting minimum stock levels
The financial impact of accumulating inventory and increasing demand variability have forced many companies to reconfigure their logistics strategy and minimise their stored stock.
This has revealed the limitations of the classic minimum/maximum stock rule. Trying to adjust it to an increasingly complex reality lies in integrating specialised logistics management software and basing decisions on measurable data.
If you want to transform your warehouse into an agile, accurate installation, don’t hesitate to invest in a WMS that’s up to the task. Get in touch and we’ll provide you with a personalised demo of Easy WMS with all the control and stock management functionalities you need.