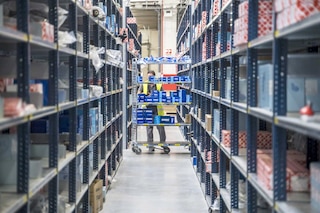
Order processing: the key to efficient operations
Order processing is one of the central activities of a warehouse, as the ultimate goal of logistics is to deliver the greatest number of orders at a minimum cost and in the shortest time. Costs allocated to order processing can exceed 60% of an installation’s total operating costs. Therefore, reducing its impact can ensure a company’s success or just the opposite if this is not achieved.
In this post, we do a deep dive into the ins and outs of order processing with the aim of having a dynamic and productive supply chain.
What’s order preparation?
Order processing is the operation charged with preparing products requested by customers to be dispatched in the form of orders. These can be sent to end customers, to distribution centres, or to other company warehouses and stores.
The term picking is often used as a synonym for order processing, but this isn’t entirely accurate. Picking refers to the process of removing products from a unit load (such as a container) that holds more items of the same SKU and depositing these goods into another unit load (a pick cart). In other words, it involves picking and combining the items that make up a customer’s order. So, we can affirm that picking is an operation within order processing.
There’s also a significant difference between the unit load and the order unit. Products are grouped into unit loads (for example, pallets, boxes, and containers) that facilitate their handling and transfer across the stages of the supply chain. Order units, meanwhile, would be the divisions of the unit load that may be included in an order. Imagine, for example, that we have a warehouse container with 100 battery blister packs (each blister contains 4 batteries). Here, there’s 1 unit load (the container), 100 order units (you can only buy blisters, not individual batteries) and 400 product units (the batteries).
Types of picking
When setting up an order processing process, it’s essential to determine how the operators receive the products, as this conditions the storage systems to be installed. Nowadays, various order processing criteria are used, and all of them can be combined or applied individually:
- Person-to-product: operators move around the installation, on foot or with the help of handling equipment, to the corresponding positions to pick the products that make up each order.
- Product-to-person: this is the quintessential criterion for automated warehouses. Operators remain at their pick stations as the goods are brought to them automatically (thanks to miniload systems and conveyors for boxes).
- Cross-docking: the goods received are directly dispatched, without having to be stored or doing so for a very brief period of time.
What’s the secret to efficient picking? Choosing the most appropriate solution that best suits the needs of each warehouse.
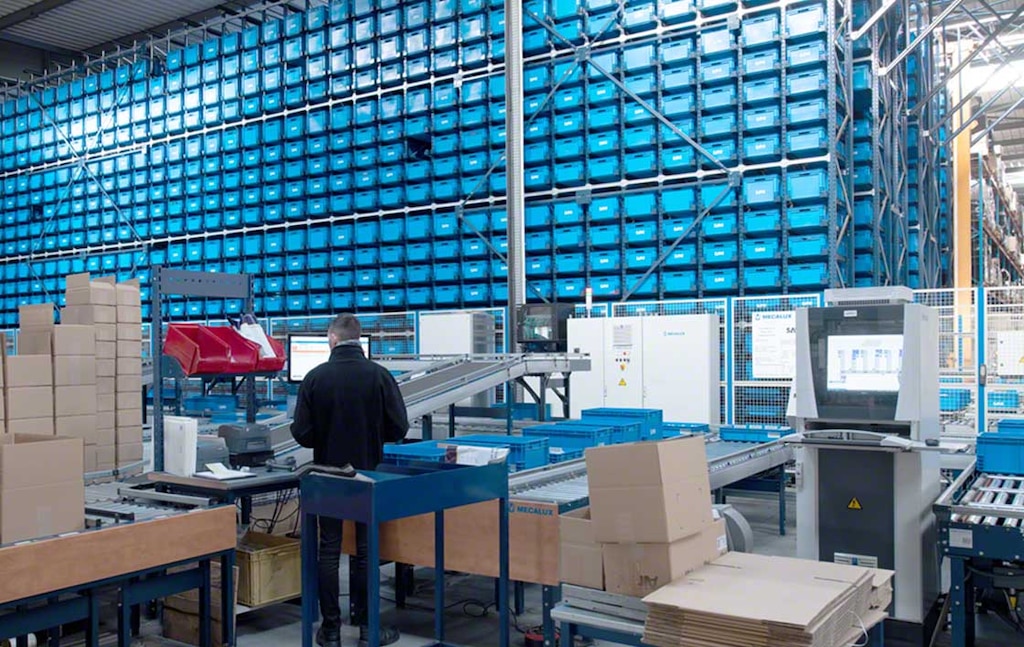
Designing a warehouse around order processing
The layout of an installation is subject to the number of orders prepared daily and to the variety of SKUs. Depending on the number of orders required, the following should be taken into account:
- Picking area: to define how the picking zone should be set up, it’s crucial to analyse the characteristics of the actual orders, the size and weight of the unit loads, the distances the operators have to travel, and the location and position of the goods.
- Racks: when designing a warehouse, one of the priorities of any company is to optimally manage high-turnover products. According to the ABC analysis, type A items should be placed in storage systems that offer direct access in order to make this operation more agile.
- Packaging: this refers to the container used to temporarily store the product(s) that have been picked. This needs to facilitate the handling and transportation of the items.
- Picking assistance devices: voice picking, pick-to-light, put-to-light, and high-throughput pick stations are ideal for minimising errors, as they tell operators where to pick products and in what quantity at all times.
- WMS: implementing a warehouse management system (such as Easy WMS from Mecalux) ensures efficient order processing. It also optimises picking routes, distributes the goods based on needs, digitises information management, and so on.
The most common practice is to combine several storage systems and order processing methods to optimise processes and make the most of the work of the operators.
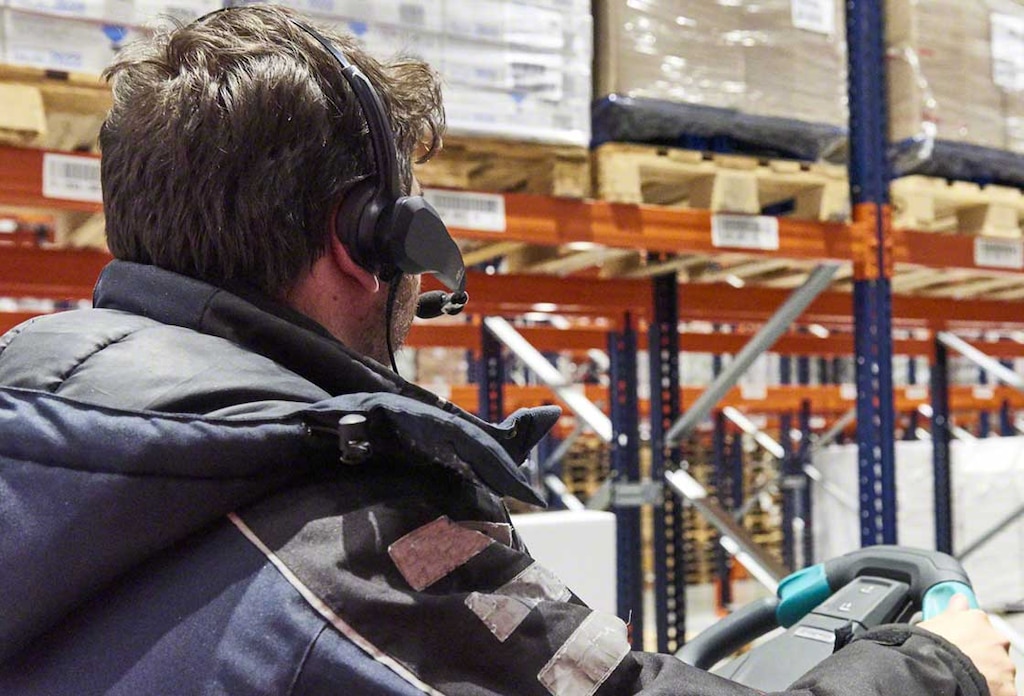
Order processing phases
It’s impossible to have a successful supply chain without knowing the phases involved in order processing:
- Prior planning: this is basic for managing and assigning available resources. If you have a WMS, the software itself prioritises the purchase order and defines the distribution of tasks.
- Travel and movements: most time and resources are allocated to this process, provided the product-to-person criterion is applied. Your best ally is an efficient warehouse layout.
- Picking or extraction of goods: this is where most mistakes are made in the picking processes. An up-to-date inventory, with the help of RFID terminals or other assistance devices such as voice picking, among others, lowers the error rate.
- Order verification and preparation for dispatch: the last picking phase deals with the verification of the units picked, order packaging and transfer to the dispatch area, printing of related documentation, etc.
The various order preparation phases carried out in an installation can vary depending on the type of product, order preparation method, or the characteristics of each order.
Logistics documentation for order processing
Orders are accompanied by basic documentation that guarantees their preparation, monitoring, and delivery to the final destination:
- Picking list: also known as a pick list, this document details the products, quantity, location, aisle, rack or shelf, and path required by the operator charged with preparing the order.
- Delivery note: this is a business document that enables the recipient to check that the contents received match those ordered. For the vendor, it constitutes proof that the buyer has received the order, and for the carrier, it substantiates delivery of the order. Nowadays, more and more businesses are working with electronic proof of delivery (ePOD) to digitally control all information relating to order deliveries.
- Packing list: relevant in the packing stage, this document details the products in the parcel as well as their characteristics.
- Road map: this indicates to the transportation agency the order delivery destinations, organised in advance by delivery route.
- Tracking number: this number is used to identify and monitor shipped orders, from the time they leave the warehouse until they reach the customer.
Automatic and digital management of all documentation is one of the huge advantages of a WMS such as Easy WMS, which, for instance, automatically creates pick lists. Meanwhile, the Multi Carrier Shipping Software module prints labels that are compatible with the major transportation agencies and assigns tracking numbers to each package directly from the installation.
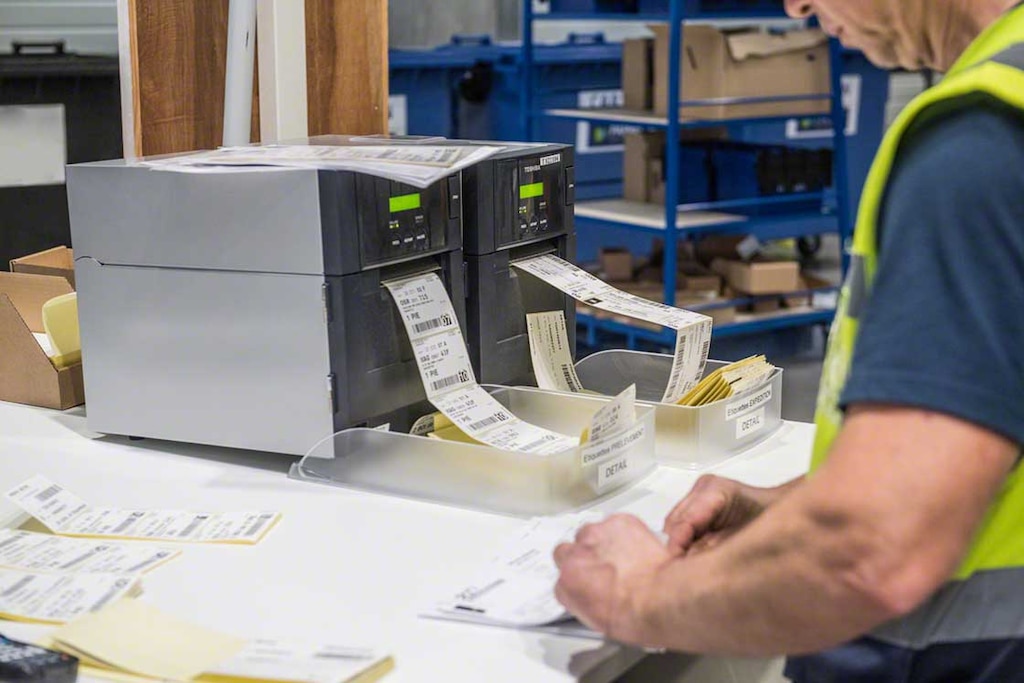
Mistakes and accidents in order processing
There are, in fact, errors made in order processing. It’s important to reduce them as much as possible to minimise their consequences, save costs, and improve the company’s image. Below are the most common ones:
- Improper product handling: this normally happens when an item is placed in the wrong location.
- Picking of incorrect quantities: this can cause inventory imbalances and mistakes in orders.
- Products of a single SKU scattered throughout the warehouse: it’s a tremendous waste of time when an operator has to go to different areas in the installation to pick various units of the same merchandise.
- Unlabelled items: if the warehouse products are stored without labels, they need to be reprocessed and labelled before being used for picking.
- Overstraining: this is one of the most frequent kind of accidents. Handling heavy goods from a non-ergonomic position can cause physical injury.
Several factors can lead to errors and/or accidents during order processing. Recognising them is the first step towards success. To minimise them, it’s advisable to use automated storage and management systems.
KPIs for measuring throughput
Warehouse management software, such as Easy WMS’s Supply Chain Analytics Software and Labor Management modules, allow you to configure KPIs (key performance indicators) to measure your installation’s throughput. This enables you to find inefficiencies that hinder operations and stand in the way of maintaining an optimised warehouse. Several supply chain KPIs will help to determine whether your order processing operations are truly efficient or, on the other hand, they could be improved:
- Productivity KPIs: these analyse and calculate process efficiency, measuring actual production compared to the resources allocated.
- Time-related indicators: these have to do with reaction time in the execution of any operation.
- Quality KPIs: these calculate, for example, the percentage of orders delivered to customers on time and of mistakes made, among other data.
- Internal order cycle time: this determines the time it takes to complete an order, from the moment the installation receives the purchase order until the parcel leaves via the loading dock. The internal order cycle time is the difference between the order entry date and the dispatch date.
Given the importance of picking throughout the supply chain, it’s critical to work with KPIs to assess the effectiveness of order processing in each of its phases.
Digital management of order processing
The management of processes, resources, and documents involved in order processing is more efficient under the control and supervision of a warehouse management system. This is even more true against the current backdrop, in which e-commerce has led customers to demand faster and error-free deliveries.
At Mecalux, we’re experts in speeding up order processing with the most sophisticated storage, picking and warehouse management systems on the market. If you’re thinking about revamping your order processing operations to adapt to the omnichannel retail challenge, or you simply want to make them more efficient, contact Mecalux. We’ll help you find the right solution for a highly competitive supply chain.