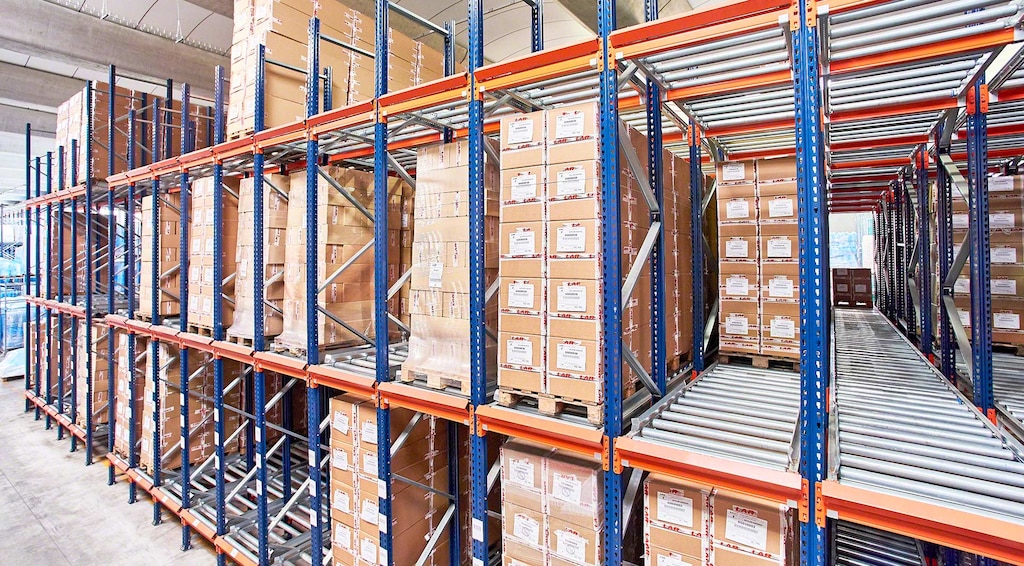
Pallet Flow Racking
High-density, space-maximising storage solution for pallets in which loads move by gravity.
The product
Pallet flow racking system: agile operations and perfect FIFO turnover
Pallet flow racking consists of high-density storage structures formed by slightly sloped channels with rollers that enable pallets to slide into place. Palletised loads are inserted in the highest part of the channel and move by gravity to the opposite end, where they are ready to be removed.
There are no intermediate aisles in a flow rack system, which increases storage capacity. In addition, the flow through racking can work in line with the FIFO (first in, first out) strategy, facilitating efficient inventory management.
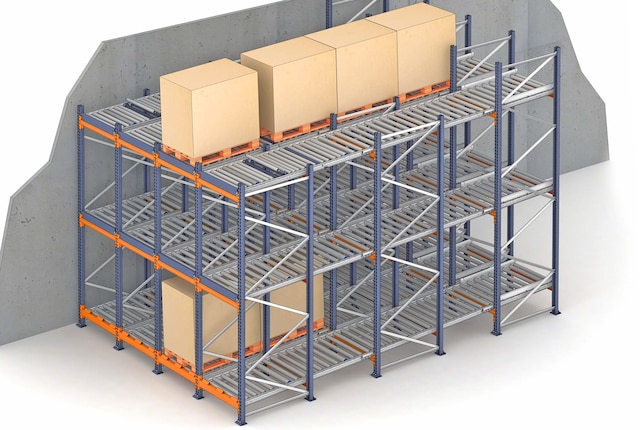
Advantages of pallet flow racking
- Maximum utilisation of surface area: pallet flow racking is a high-density storage solution that significantly increases a warehouse’s capacity.
- Flawless product turnover: its compatibility with the FIFO method fosters excellent inventory control.
- Time savings: having all SKUs available in a single working aisle makes it easy to locate any product, reducing forklift manoeuvring time and speeding up pallet removal.
- Separation of loading and unloading: pallet storage and retrieval are performed from separate aisles. This eliminates interference and enables forklifts to work without interruptions.
- Multiple SKUs: although each channel houses a single SKU, these can vary between the different channels.
- Better energy consumption: implementation of this system in facilities run at low temperatures reduces energy consumption since the volume to be cooled is smaller.
- Safety and reliability: the different elements that make up Mecalux’s pallet flow racks are designed to ensure risk-free operation for operators and goods.
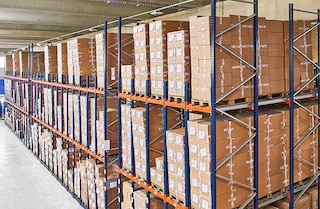
With the pallet flow rack, we’ve shortened the time it takes to insert and remove pallets from the racks by 50%
Pallet flow racking system applications
Ideal solution for multiple industry and distribution sectors
Pallet flow rack systems are perfect for companies that need to make the most of their available storage space and streamline goods handling operations for efficient, error-free inventory turnover.
How does a pallet flow racking system work?
Perfect stock control with minimal movements
Gravity flow racks are characterised by their extremely simple operation. Their structural configuration fosters remarkably agile management that shortens manoeuvring times and reduces the distances travelled by forklifts. The result? Fast storage and retrieval operations.
Case studies
See more case studiesPallet flow racking configurations
Highly versatile storage solution adaptable to diverse needs
Gravity racking systems can be configured in several ways. This depends on the required goods management method and the type of operations to be performed, e.g., order picking from the racks themselves.
Pallet flow racking components
The manufacturing quality of the different components used in Mecalux’s pallet flow racking makes the system highly reliable, ensuring the correct operation of the system and a long service life.
Live racking is formed by elements common to all types of pallet racking (frames, beams, etc.) as well as components specific to gravity racking systems, e.g., roller tracks.
The gravity flow racks integrate a set of components that ensure the safe, speed-controlled movement of the pallets inside the storage channels.
Gravity racking accessories
Set of elements used to adapt the system to specific needs.
Catalogues

Pallet flow racking (catalogue)
Perfect turnover rotation thanks to the movement of pallets by gravity
Download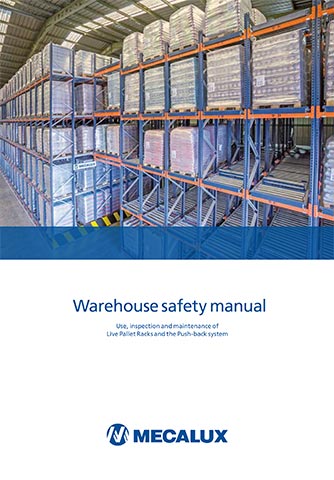
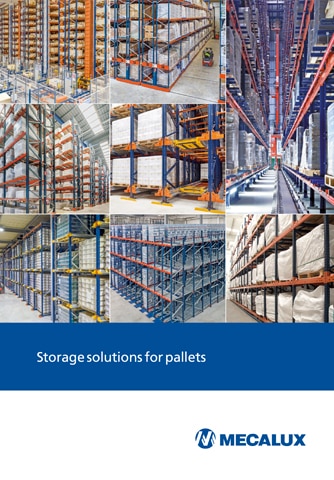
FAQs
Pallet flow racking — also known as pallet live storage, gravity racking, and FIFO racking system — is the most agile high-density pallet storage system on the market. It comprises racks containing sloped rails with rollers upon which the loads slide. Its structure leverages gravity to streamline loading and unloading operations. In addition, the absence of interior work aisles increases the utilisation of the available storage space.
Pallet flow racks have multiple benefits. First of all, they are the most agile high-density storage system with the best operational performance, making them an ideal solution for different types of warehouses. Likewise, their implementation ensures excellent inventory control. Moreover, the separation of the loading and unloading aisles eliminates interference, and the existence of a single SKU per storage channel facilitates product location and reduces extraction times. The pallet flow rack also guarantees maximum use of the available surface area, although the installation of deep channels could entail a certain loss of capacity in height (a slope of approximately 4% is required for the system to function correctly).
One of the main differences between the two systems lies in the characteristics of their respective loading and unloading operations. In a drive-in/drive-through racking system, the forklift enters the storage lanes to deposit the pallets. With pallet flow racking, on the other hand, the forklift does not drive into the structure. Instead, it places the pallets at the entrance to the selected storage channel, and they slide into their locations in a completely autonomous way. Therefore, in pallet flow racking, storing and retrieving loads is significantly safer and more agile. Another notable difference is the variety of SKUs that can be stored. The number is substantially higher in gravity racking, as each channel can store a different SKU. In drive-in racking, however, all channels of a single storage lane must house the same SKU.
The main difference between these two types of racking systems is related to the inventory management method associated with each one. The pallet flow rack has two working aisles (one for loading and the other for unloading) and operates according to the FIFO (first in, first out) principle. Thus, the first pallet deposited in a channel is also the first to be removed. Push-back pallet racking, on the other hand, works in line with the LIFO (last in, first out) method. With only one working aisle, the last pallet stored in a channel is the first to be retrieved. In warehouses that manage perishable goods (e.g., food or pharmaceuticals), the pallet flow rack is the ideal alternative, as it prioritises the removal of products with the closest expiry dates.
In pallet flow racking, storage channels can accommodate up to 30 pallets in depth. Nevertheless, it is important to note that implementing very deep channels could reduce storage capacity in height. This is due to the angle of inclination required for the system to work properly.
Each storage channel is sloped at an angle of approximately 4% to guarantee that the pallets slide smoothly and safely.
The spacing between uprights — in other words, the length of the beam — should be equal to the front dimension of the pallet including the load plus 160 mm of space (i.e., 80 mm on either side). Otherwise, the pallet or goods could hit the rack frame.
No. Mecalux pallet flow racking leverages the force of gravity to enable pallets to move inside the slightly inclined storage channels.
This simple system includes a pedal that moves rods that lower or lift the retainer to hold back the second pallet. When the first pallet reaches the exit point, its weight presses against the pedal, which drives the movement of the rods. The rods activate the retainer, which prevents the second pallet from continuing to advance toward the end of the channel, avoiding contact between pallets.
Pallets are usually handled from the narrower side and move inside the channels with their bottom deckboards perpendicular to the rollers. In shallow channels, pallets can be handled from the wider side. That is, they move along with their bottom deckboards parallel to the rollers. In this case, as the rollers occupy the entire width of the channel, they can be replaced with three sets of short rollers.
With pallet flow racking, it is possible to work with any type of forklift (counterbalanced, reach trucks, VNA trucks, etc.).
Yes, the pallet flow rack can be served by stacker cranes for pallets that fully automate storage and retrieval operations. This automation can also be partial, affecting only one operation. In fact, many times, a single stacker crane is installed to store pallets, while operators remove pallets in the opposite aisle using forklifts.
Ask an expert