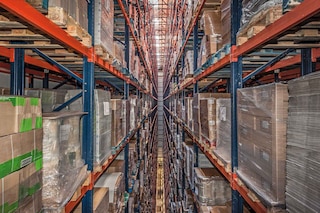
Reorder point formula: how does this affect warehouse management?
The reorder point (ROP) refers to the moment a company has to place a new order for stock with its suppliers in order to avoid a stockout.
When organising the replenishment of warehouse stock, you need to ask yourself two fundamental questions: When should you place a new order? How much of each product should you purchase?
The responses vary depending on the stock management model applied. In our article, we’ll explore all you need to know about the reorder-point formula and concept.
Deterministic and probabilistic inventory management models
When managing a company’s stock, major factors affecting calculations are the nature and variability of the demand. There are two main models:
- Deterministic inventory management methods
This methodology is based on the premise that demand is known and has a constant and, therefore, predictable rate of consumption; (however, in reality, unforeseen events that distort demand trajectory will always arise). Demand can be static (stable over time) or dynamic (with seasonal peaks and valleys).
The Wilson model, one of the first inventory management methods, belongs to this category. Since it assumes constant demand throughout the year and fixed prices regardless of volume, it’s a completely deterministic model.
Although these stock management formulas are more classic and easier to apply, they’re the ones that least reflect the complexity of real demand.
- Probabilistic (or stochastic) stock management methods
According to these models, there is no exact or constant value that defines demand; however, demand calculations and predictions can be made from probability functions that vary over time.
These forecasts come closer to reality, but they involve more complex calculations. Because of this, software specialised in advanced demand forecasting techniques is normally implemented. Likewise, these probability functions based on sales performance could follow a constant pattern or be subjected to seasonal fluctuations.
Both the deterministic and probabilistic models for predicting demand will directly impact the reorder point formula.
Reorder point formula for replenishing stock
The objective of the reorder point is to achieve a balance between the goods investment cost and the risk of a stockout. The reorder point can be scheduled regularly (e.g., on a certain day of the week) or can be kept under continuous review.
Most companies choose the second option, since it’s more flexible. Plus, it takes into account product diversity and demand variability over time.
To calculate the reorder point, it’s necessary to bear in mind the following factors:
- Safety stock levels established to prevent stockouts. This is related to the level of service accepted within the company.
- Supplier lead time, or the time it takes the supplier to manage an order and ship the goods. It can also refer to the time needed to manufacture the merchandise. If purchase orders are issued to various suppliers, you have to consider all the lead times and, most likely, set various reorder points.
- Expected consumption of this product per the corresponding time unit (usually days). As seen above, these forecasts can stem from deterministic or probabilistic methods. Nevertheless, in both cases, this is a crucial factor when calculating the reorder point.
The following is the reorder point formula:
Reorder point (ROP) = safety stock + (average consumption x supplier lead time)
Let’s illustrate this with an example. A company has a daily demand of 500 units and the supplier’s lead time is 5 days. The safety stock for this SKU is established at 100 units. The reorder-point calculation would be:
Reorder point (ROP) = 100 + (500 x 5) = 2,600 units
This indicates that the firm needs to purchase new goods when stock in the warehouse goes down to 2,600 units. This way, demand will be covered during the time it takes the supplier to send new product.
Simplified representation of the reorder point
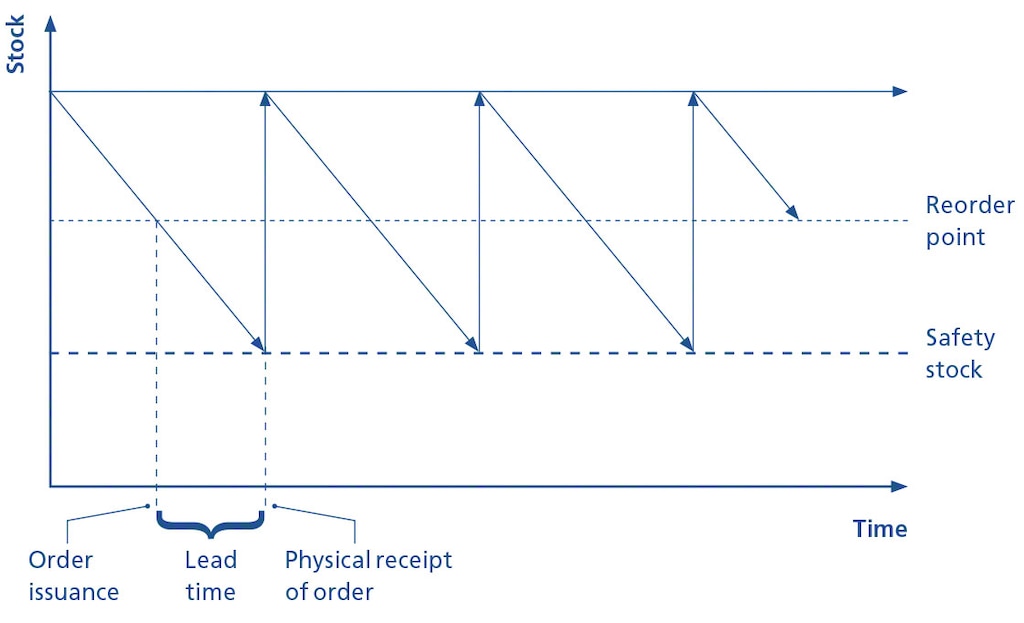
Reorder points from a warehouse perspective: guaranteeing accuracy
The reorder points set the business’s replenishment policy into motion. Coordination between available inventory in the installation, the order and the subsequent receipt of goods should be seamless, the objective being to prevent imbalances that compromise storage capacity and the financial investment allocated to the stock.
So, how does the warehouse contribute towards the accuracy of the reorder-point calculation? Here are some strategies that facilitate procurement management:
- Store reliable stock data
Every installation keeps a computerised stock record with data on available goods. Most often, the ERP contains this information, which is used by the rest of the company’s logistics areas.
The warehouse needs to be sure, then, that the data reflected are exact and up-to-date to prevent the reorder point from being calculated incorrectly and leading to serious discrepancies.
One huge advantage of using a WMS in your installation is that stock control is continuous, as all goods movements are recorded as they’re produced, in real time. This makes it easier for logistics and purchasing managers to know what stock is available in order to plan the reorder points.
In addition, if it’s necessary to conduct counts or take inventory periodically, a WMS such as Easy WMS will support you throughout the entire process, ensuring that it’s done as quickly as possible and with the utmost accuracy.
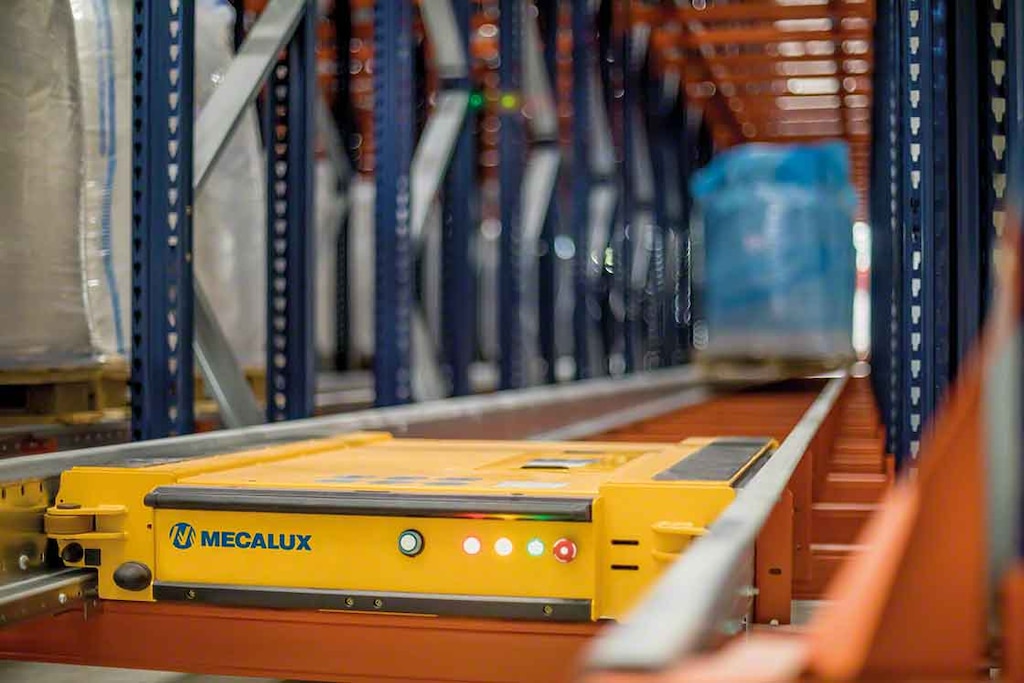
- Monitor supplier and warehouse lead times
When you reach the reorder point and issue an order, you normally have to anticipate the goods that are on the way while those in the installation continue to be consumed. The reorder point is meant to be unique for each SKU.
However, the calculation can become complicated if the company follows a multi-supplier policy, whereby orders are sent to various suppliers to obtain products belonging to a single SKU. This is usually done to optimise the purchase of new stock and suppliers often offer different delivery times and prices due to their location.
In such cases, you have to take the calculation of the reorder point a step further and adjust it to demand, setting various reorder points. For instance:
- First reorder point: this would trigger an order sent to the supplier with a later delivery date but better prices (this supplier is usually chosen because of the cost reduction).
- Second reorder point: an order would be sent to the supplier with the shortest lead time, which could be a local one. This would be activated when the installation is at the greatest risk of a stockout.
On the other hand, to fix these reorder points, you also have to take into account the operating times the warehouse needs to manage the receipt and replenishment of the goods.
If deadlines are down to the wire, the warehouse management system will prove decisive in preventing stockouts, since this software:
- Helps prioritise tasks according to logistics parameters such as transport routes and delivery dates.
- Facilitates the organisation of goods receipt, quality control and stock replenishment.
- Allows the replenishment goods to be sent directly to picking area or cross-docked.
Adaptability and speed, the keys to optimal warehouse management
The reorder point triggers the resupply of product in the installation. When managing stock replenishment, it’s vital to deal with appropriate times and quantities so as not to overstock your warehouse and overwhelm operations.
Warehouse management systems play a central role in being able to react reliably, as they ensure the adaptability of the working method and speed of response.
Thanks to modules such as Supply Chain Analytics Software, warehouse and logistics managers can view the status of each operation, including information on reorder points such as: the customer panel (percentage of SKUs with stock, percentage of pending orders, on-time deliveries and cycle times) and the warehouse capacity panel (location use, volume occupied per location type, slots used per article type, etc.).
To explore all the advantages a warehouse management system can offer your installation, get in touch — we’ll provide you with a detailed demo on the functionalities of our Easy WMS.