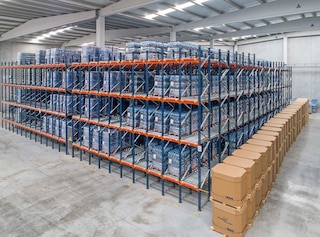
Live racking systems: types and characteristics
Live racking systems consist of very particular types of high-density racks: their components and structure leverage gravity to streamline all goods extraction and storage operations.
These structures save time compared to traditional drive-in/drive-thru racks, as the fork trucks don’t need to enter the lanes (gravity forces the products to slide forward towards the front of the racks). They’re also known as gravity live systems.
When choosing a specific type of live rack, it helps to consider the advantages each one offers and understand the applications of this system in the various areas of your warehouse.
What’s a live racking system? Characteristics
What sets these live storage systems apart is the incorporation of rollers or trolleys with bearings that facilitate the controlled movement of goods from one end of the channel to the other.
The inclination of the roller platforms can be personalized depending on the unit loads: it’s usually set at a 3% to 4% angle for pallets, while it can be higher for boxes.
On that basis, let’s take a look at some typical questions:
- What height can live pallet racks reach?
This isn’t a storage system that stands out for its height, although it is possible to combine it with stacker cranes for pallets. To operate with these kinds of racks, manual handling equipment is normally used, limiting the height.
On the other hand, it should be noted that, due to the inclination of this system, the live pallet racks are taller than traditional high-density systems. What’s more, the higher their levels, the greater the loss of storage space (which could even amount to an additional level).
- What security systems do they have?
Without some kind of control mechanism in place, the force of gravity acting on heavy loads can be problematic. That’s why live pallet racks are equipped with the following elements to ensure safe load handling:
- Brake rollers: slow down the speed of the load depending on the force generated. The faster the acceleration, the greater the brake force.
- Pallet centralizers: assist with pallet entries to ensure they fit perfectly in the channel.
- Ramp stops at the ends of the channels: reinforce this area to prevent it from giving way to the accumulated weight of the goods at the exit point.
- For which types of goods are live racking systems suitable?
Depending on the type of live racking system, it could operate with FIFO or LIFO goods flows, as we’ll see below in more detail. In any case, the main feature of live pallet racks is increased agility as compared to high-density racking, since they save time on movements and pallet extraction operations. Consequently, this system is indicated for storing medium- and high-turnover goods.
In addition, these structures are adaptable to different unit loads: pallets of varying sizes, half pallets, metal containers and boxes (in picking).
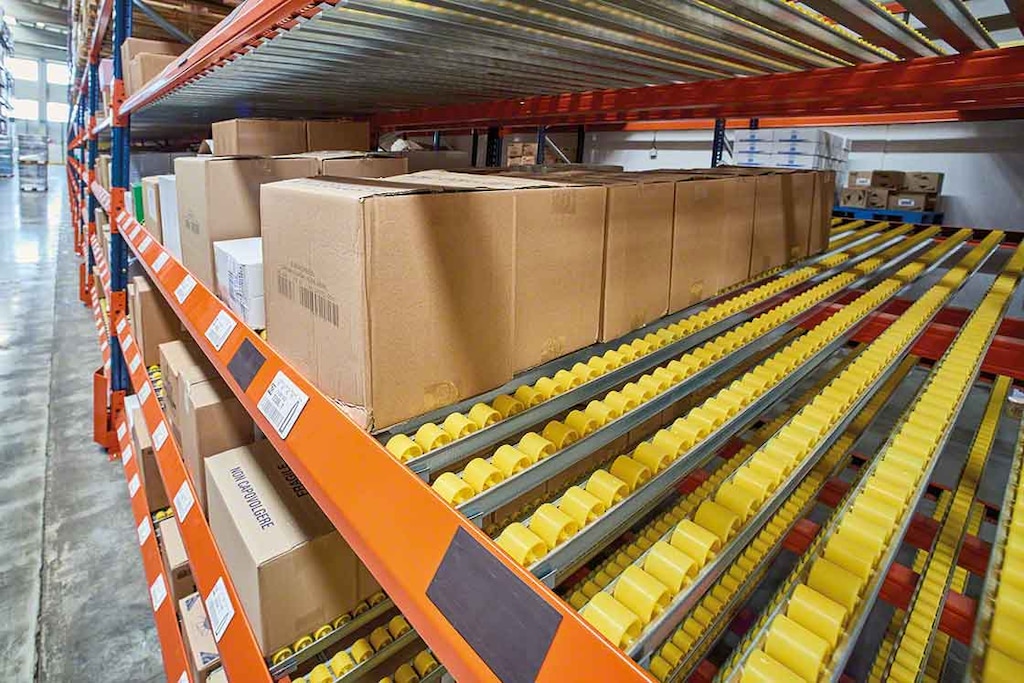
Types of live racks
Generally speaking, high-density systems are ideal when there are many unit loads of a single SKU and turnover isn’t a priority. However, live pallet racks can, indeed, be employed with goods with a higher turnover. In fact, that’s their main advantage and attribute.
The gravity live storage system is implemented in various types of racks that have the same conceptual basis but differ in certain aspects. Let’s take an in-depth look at them:
1. Live pallet racking with rollers (FIFO)
These are the most commonly used racks. Live racking systems with rollers require two aisles: one to insert pallets into the corresponding channel and another to extract them.
Thanks to this separation, incoming and outgoing traffic remains uninterrupted, while forklift operators gain in maneuverability. Plus, a safety aisle is usually included in the middle of the live racking unit for use in an emergency.
Apart from these three aisles, no others are necessary, making the savings in storage space remarkable. This can be seen in a warehouse Mecalux designed for snack producer Tosfrit.
Each level of a lane stores a different SKU, as with all high-density systems. When a new pallet is inserted, it glides from one end of the channel to the other due to the force of gravity and the rollers. When the first pallet is removed at the exit point, the second pallet moves forward, taking its place.
So, these racks are perfect for handling goods according to strict FIFO criteria (first in, first out). They’re commonly used in perishable-goods warehouses and for merchandise with continuous entry and exit flows, that is, high-rotation products.
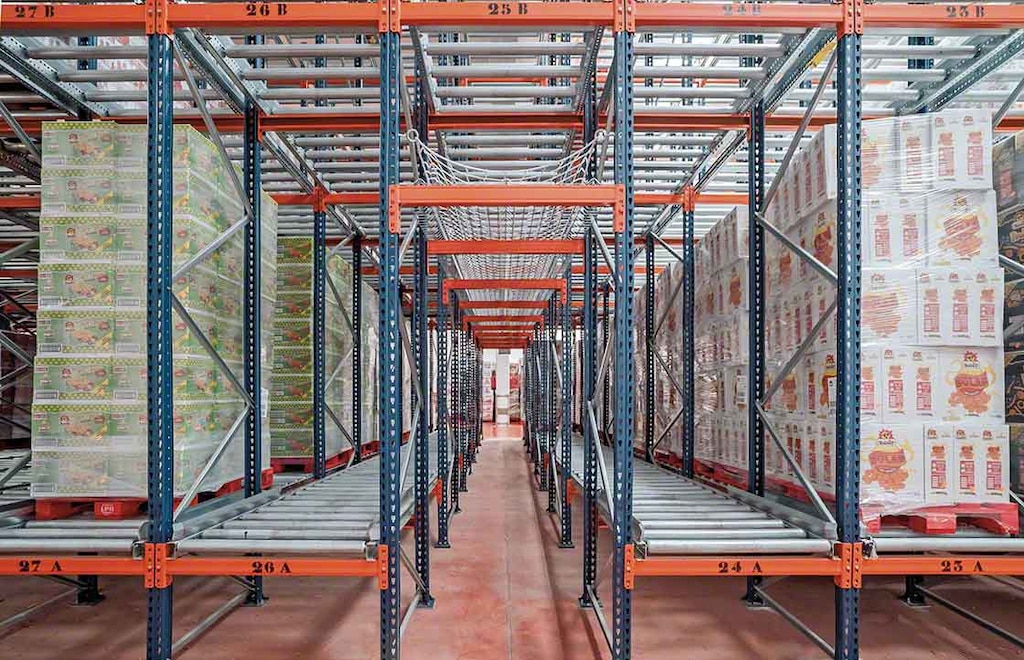
2. Live pallet racking and automated systems
Live racks with rollers can be installed with stacker cranes for pallets, thus, serving as the base storage system for an automated warehouse. It’s not a usual combination, but it goes a step further from double-deep racking, since several pallets can be added depth-wise.
In the end, it’s a solution halfway between pallet racking with stacker crane and pure high-density automated storage with Pallet Shuttle and stacker crane (the force of gravity replaces the Pallet Shuttle mechanism).
3. Push-back pallet racking (LIFO)
In the case of push-back pallet racks, pallets are loaded and unloaded from the same end in such a way that only a front aisle is necessary. This saves a huge amount of storage space, although you have to bear in mind that each level of a lane is reserved for a single SKU.
As a result, these racks are used with loads handled in line with LIFO flows (last in, first out) and that have a medium turnover (they’re not as agile as live pallet racks with rollers).
The structure of this type of live racking system is made up of carts and rails. The handling equipment pushes the incoming pallets into the channel, while gravity itself then draws them forward towards the channel’s front position. Structures incorporating rollers can accumulate up to six pallets deep.
This system streamlines the loading and unloading process, which can also be carried out with standard forklifts. These advantages actually led Desert Depot USA to choose this type of live storage system at its warehouse equipped by Mecalux.
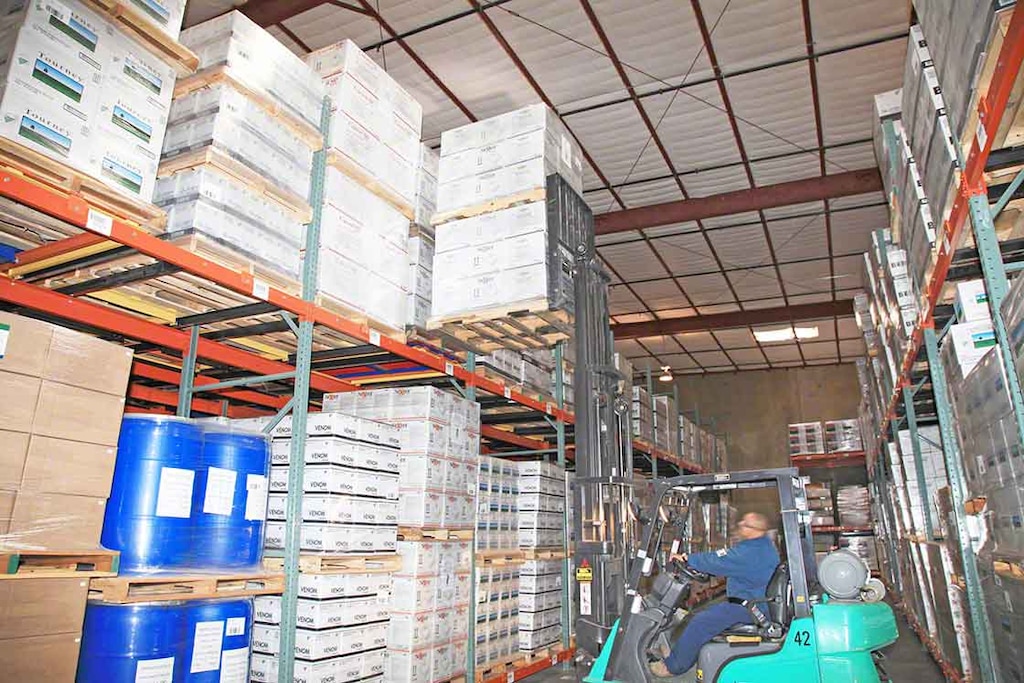
4. Carton live storage for picking with rollers
Gravity live systems are also important when it comes to speeding up the picking and order prep process for goods with a very high turnover that follow FIFO criteria. These racks are incorporated with wheels or rollers that move the boxes to the output end. Live storage for picking are designed to:
- Shorten picking travel times: as each level stores a single SKU, operators simply have to move in a straight line, perpendicular to the carton live storage.
- Increase storage space: the channels can accumulate SKUs in depth whenever there are many boxes per SKU, making it possible to gain 30% more in storage capacity.
- Free the picking area from interference: since the racks are replenished from one side, order prep isn’t interrupted on the other.
It’s also common to find them used in combination with assistive picking devices such as pick-to-light systems and automatic ones such as roller conveyors for boxes.
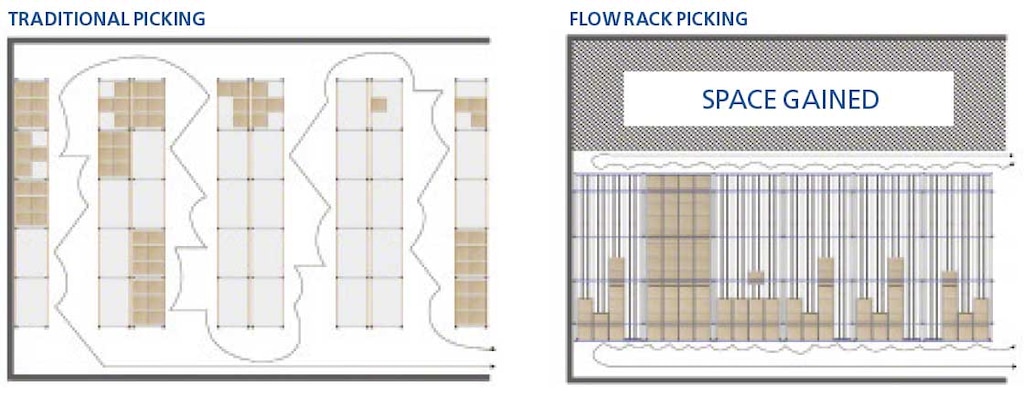
Live racking systems: key applications
- Perishable-goods warehouses: most live racks are extremely useful when goods flows follow strict FIFO criteria and have a high turnover. They’re frequently seen in the installations of large food distributors.
- Interim storage areas, between work zones: especially in the case of live racks with rollers and carton live storage, they serve to connect the dispatch and storage areas by leaving the aisles free on both sides.
- Temporary storage: for example, the gravity live system is used in the accumulation channels for dispatches when they are in the staging area. Live storage racks, therefore, work as buffers for dispatches and production.
When equipping your warehouse, it’s advisable to have as much information as possible regarding the logistics parameters at play in order to decide which storage system is optimal.
If you’d like us to help you make the calculations in detail and determine whether live racking systems are the most suitable in your case, don’t hesitate to contact us. One of our specialists will be happy to advise you.