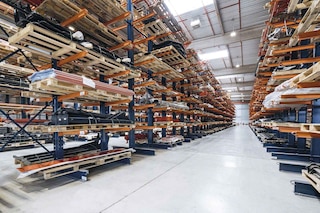
What’s a MES? How does it differ from an ERP and a WMS?
With the arrival of Industry 4.0, the management of warehouses and production centres needs to be perfectly in sync. This is an indispensable requirement for being able to cope with increasingly more personalised products and shorter time frames for manufacturing them. MESs (manufacturing execution systems) are not new on the industrial scene. Recently, however, they have been growing more important in the implementation and monitoring of production.
MES software was introduced at the beginning of the 1990s following increased competition in the manufacturing sector and cutbacks in profits, which limited the generation of large (and costly) inventories. What are the main functionalities of manufacturing execution systems? How do MESs relate to ERPs and WMSs? We’ll analyse this in depth below.
MESs (manufacturing execution systems) defined
A MES (manufacturing execution system) consists of software designed to organise, control and monitor production centre processes, achieving maximum efficiency and cost reduction.
MESs also generate extremely useful data for the overall analysis of a company’s production management, as they’re integrated with other systems such as ERPs (enterprise resource planning software) and WMSs (warehouse management systems).
MES software characteristics and functionalities
The origins of MESs date back to MRP (materials requirement planning) systems, which controlled the flow of materials that supplied production centres in the 1960s and 1970s. These first systems were very inflexible, hence the evolution towards MRPII systems, which incorporated functionalities that sought to overcome the main limitations of its predecessors. MESs further this development and are capable of managing a greater number of processes, such as:
- Sequencing of manufacturing activities based on the priorities and characteristics of each production batch. The MES oversees the work in the centre and supervises its execution to detect irregularities.
- Monitoring of work in progress (WIP), or ongoing tasks forming part of the production process, to ensure that the established schedule is met and to prevent bottlenecks.
- Automatic data capture and document management, as the MES gathers data on processes, materials and operations performed by workers and machines.
- Process throughput analysis, following performance in real time and comparing it with historical data. This also includes the assessment of resources devoted to each task, cycle times, adherence to planning and costs.
- Quality control, which cross-checks the status of finished products with semi-finished goods to verify that they are progressing as scheduled. In addition, this measures process quality and, if errors are detected, the MES recommends corrective actions.
- Maintenance tasks, as the MES software contains all the information related to the operation of the machinery. It issues an alert when there are malfunctions and assists in diagnosing the causes.
- Assignment of tasks to production centre staff to make sure the workloads are evenly distributed.
MES, ERP, WMS: what’s the difference?
Manufacturers use MESs to regulate and optimise the operation of their production plants, but what’s their place in the network of systems working within a company? In this diagram, we sum up the way in which these systems are organised:
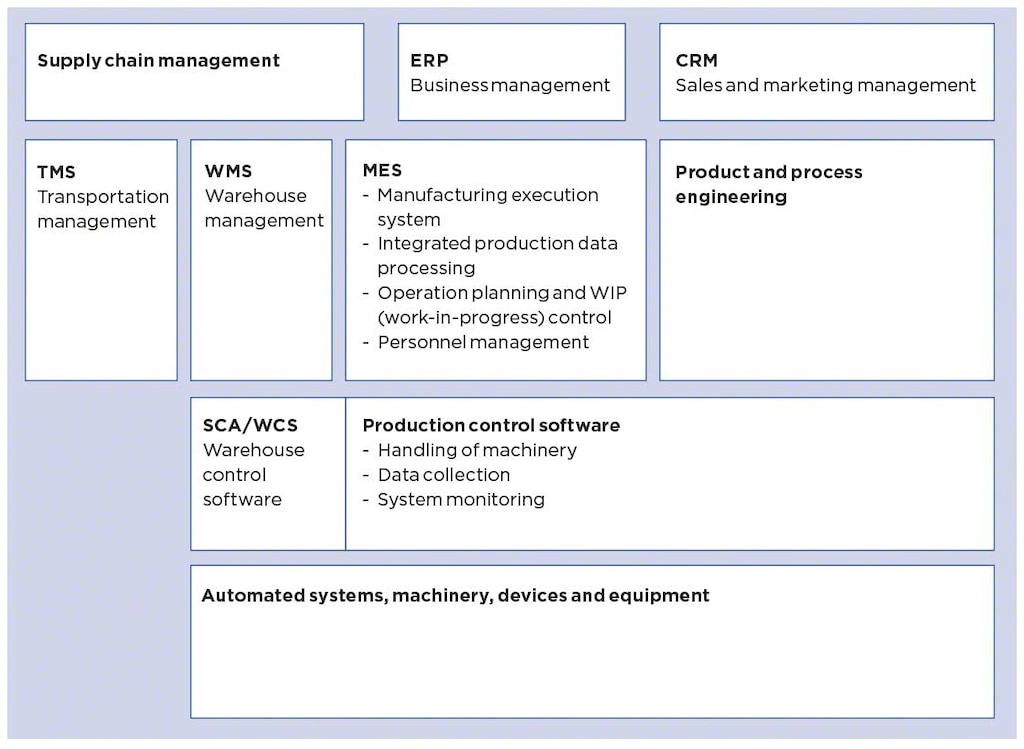
We’ve already written an article to discuss the differences between an ERP and a WMS in depth, but let’s run through their characteristics and definitions compared to those of manufacturing execution systems:
- Difference between a MES and an ERP
The ERP serves as an umbrella for the other systems, including the MES. It controls all business management processes but is not specialised in production management in manufacturing plants. Both the MES and ERP operate in an integrated way and communicate continuously. The MES, however, has much more detailed information with respect to the production lines, the machinery on which they run, the product batches they generate, the traceability of these lots and process quality, among other data.
- Difference between a MES and a WMS
MES and WMS (warehouse management system) software work in sync to guarantee that material flows from the installation to the production centre and vice versa occur without interruptions and with maximum efficiency. The WMS manages the BOM (bill of materials), that is, the database of all components linked to production. Therefore, a WMS for manufacturing controls the available stock in real time and coordinates with the MES to supply the production lines.
MESs and WMSs: how are they related?
The MES serves as an intermediate layer between the ERP and the production plant and works at the same level as the WMS. However, it’s necessary to have a warehouse management system with functionalities designed specifically for manufacturing logistics.
This is the case with Easy WMS and its manufacturing module, which is configured to:
- Carry out the physical management of parts or materials that need to be supplied to production centres.
- Operate with finished goods sent by the manufacturing plants, register these products and prepare them to be dispatched.
Integrated with MESs, WMSs for manufacturing carry out the following:
- Classify the inventory by status and control its traceability
WMSs for production not only include the BOM (bill of materials), or list of components and raw materials supplied to factories, but also control the traceability of the entire inventory, including semi-finished and finished products. Moreover, material flow control is enhanced when the WMS operates with automated systems such as stacker cranes and conveyors; their control software informs the WMS of the location of each SKU in real time.
- Manage formulas and production orders
Formulas define the raw materials and quantities required to manufacture a specific product. These can be modified and customised following indications from the MES to meet the scheduled production batches and respond to any changes in these formulas flexibly and efficiently.
On the other hand, if the company receives a new order that activates one or more production lines, the WMS sends a manufacturing order to the MES software. Both systems operate in alignment, since the warehouse provides the factory with the batches of materials as they are requested in the various production stages.
- Report inventory consumption and record finished products
The WMS takes into account the different reorder points for each product to notify the purchasing department of the need to replenish stock for SKUs that have reached their minimum stock levels. The goal is to avoid those pesky stockouts that can lead to downtime on the production line.
Then, once the new finished goods arrive from the manufacturing plant, they are registered in the WMS, which assigns them a location in the warehouse. Alternatively, they are directly prepared as part of an order for a specific customer.
MESs and their relevance in Industry 4.0
MESs are essential for optimised production planning in the age of Industry 4.0, which is characterised by digitalisation and greater integration of processes throughout the supply chain.
In this context, proper coordination between the MES software and the warehouse management system eliminates major inefficiencies. Before, the lack of accuracy in supplies of materials to production centres created serious complications: there were either shortages, requiring new requests for SKUs from the warehouse, or too many goods, in which case the unused raw materials had to be returned to the installation.
WMSs solve these problems by adjusting quantities and variations in production formulas and orders as much as possible. In this way, WMSs free factories from having to manage complex and highly variable stock. Ultimately, WMSs make it possible for production centres to focus on achieving excellence in manufacturing processes, their true area of expertise.
For more information on our WMS for manufacturing, don’t hesitate to get in touch. One of our software specialists will explain its functionalities and capabilities in detail.